Condition Monitoring
Condition monitoring (CM) is the process of monitoring a particular condition in machinery, to identify changes that could indicate a developing fault. It is a major part of predictive maintenance as it allows for maintenance to be scheduled and preventive actions taken to prevent further failure and subsequent unplanned downtime.
What is Condition Monitoring?
Condition monitoring is a systematic set of processes and technologies that assesses, and monitors the condition of industrial machinery for a given time-period or environment. This is typically done through physical means, such as vibration monitoring, inert gas monitoring, or thermal.
The use of these technologies can make a huge impact in maintaining industrial machinery. It improves worker safety and reduces the chances of collateral damage to the system. Traditionally, vibration analysis was the preferred means of asset monitoring, but now modern techniques such as sensors and sophisticated softwares are being used to monitor conditions in real-time.
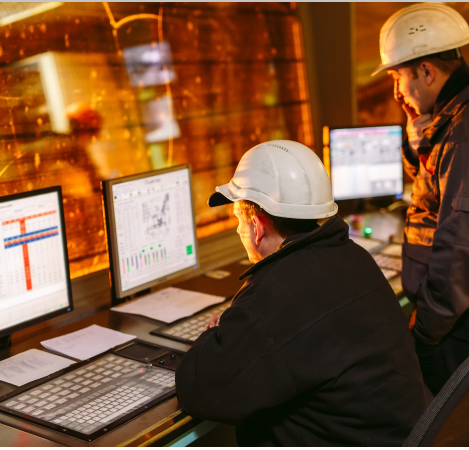
How does Condition Monitoring work?
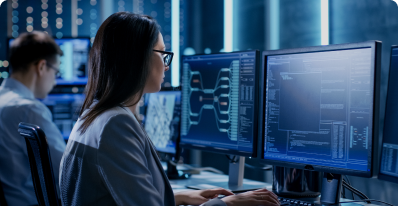
Installation
In order to monitor the condition of any machine, it is essential to collect data, which can be accomplished by installing a monitoring system. Machines / instruments are fitted to the machines to monitor their output. By collecting data on the output parameters of the machine and analyzing its performance, the CM system can detect if a machine has a fault or not.
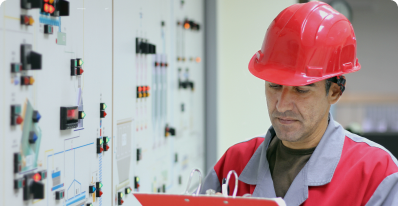
Establishing a Baseline
The system once installed correctly, can begin to collect the data to measure the performance of the equipment. This data may consist of vibration, speed, and temperature among others, which may be used to create a baseline which is indicative of ideal operating condition, against which future performance of the machine will be measured.

Condition Monitoring
Data is transmitted and evaluated by the condition monitoring system from which the performance and diagnostics are evaluated. The system processes the data and notifies the maintenance and reliability professionals if any abnormality is detected, thereby enabling the professionals to take immediate action, preventing catastrophic failures.
Condition Monitoring Services
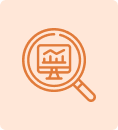
Condition monitoring services offer the promise of optimizing manufacturing operations. The demand for such services have been rising due to the increased focus on overall plant & machine health as well as breakdown monitoring.
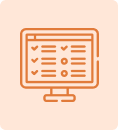
Condition monitoring is a tried & tested, effective & powerful maintenance tool that is being used by an increasing number of industries. Condition monitoring frameworks provide significant advantages from a monetary, functional and safety perspective. When used with associated systems, it allows to make the most of planned maintenance schedules, by addressing multiple problems in one schedule which otherwise may cause unplanned downtimes. One major advantage is that it helps companies to make more accurate decisions and therefore there is a high potential for companies to increase their profitability and minimise the risk of operational losses.
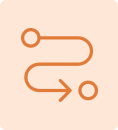
Nanoprecise Sci Corp is an automated end-to-end condition monitoring solution that offers real-time predictive information about the genuine health and performance of industrial assets. Nanoprecise specializes in the implementation of Artificial Intelligence and IoT technology for predictive asset maintenance and condition monitoring. The AI-based predictive maintenance solution monitors different parameters to provide enhanced visibility of the machine health thereby offering increased transparency to the manufacturing operation as a whole. Nanoprecise provides accurate prognostic and diagnostic solutions that predict the remaining useful life of any asset at any point during its lifetime, thereby empowering users with the right data across several industries.
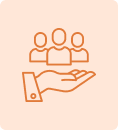
Nanoprecise works with customers across the world, in diverse sectors, to prevent catastrophic failures, saving time & money. Machine-Doctor™ sensors and RotationLF™ platform from Nanoprecise provides accurate diagnostics to customers across sectors such as steel, oil & gas, metals, mining, chemicals and pharmaceuticals among others, to help the maintenance teams identify the potential issues that could cause catastrophic failures. Nanoprecise continues to build trust with our customers by allowing the maintenance and reliability teams to identify problems and ensure that they are getting to the root cause.
Request a Call Back
Frequently Asked Questions
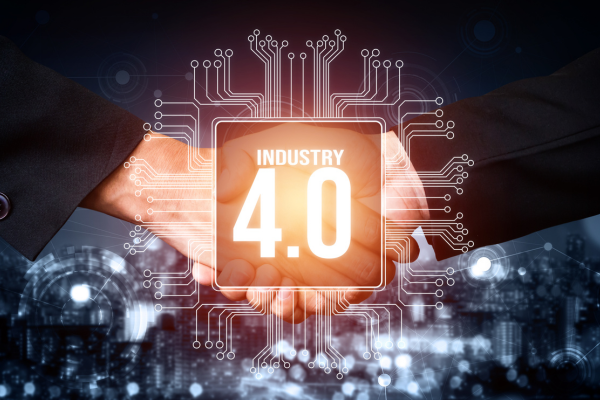
Let us show you how!
Explore the transformative potential of predictive maintenance. At Nanoprecise, we specialize in tailoring predictive maintenance to your unique needs. Reach out today, and together, let’s pave the way for a more efficient, profitable and sustainable future.